The Warehouse Inspection That Maximizes Capacity and Minimizes Risk
Keep Your Storage and Warehouse Facility Safe, Functional, and Ready to Perform
Since 2019, warehouse buildings and storage facilities have made up 9% of our total commercial property inspections across Oklahoma, Arkansas, Missouri, and Kansas. These properties serve as logistical powerhouses—whether storing raw materials, inventory, or equipment. For owners, tenants, and investors, the value of a warehouse lies in its structural integrity, operational efficiency, and code compliance.
Our inspection services help clients answer critical questions: Is this space ready for high-volume storage? Will it support expansion? Are there hidden risks that could lead to costly repairs, liability, or downtime?
The People Behind the Property
Different stakeholders rely on warehouse space for different reasons. Our job is to provide insights that match each client's operational and financial goals.
Building Owners & Property Managers
Owners need to protect the value of the facility and maintain lease readiness. Warehouse tenants often demand fast occupancy and high standards. Inspections help owners identify needed repairs before lease transitions or capital reinvestments.
Buyers & Sellers
Buyers of warehouse facilities—whether institutional or private—must ensure the space is structurally sound, compliant with fire codes, and ready to meet tenant expectations. Sellers use our reports to show transparency and prepare for smooth transactions.
Commercial Lease Tenants
For tenants leasing storage or distribution space, avoiding unknown repair obligations is key. Our inspections help tenants document pre-existing conditions, confirm loading dock function, HVAC suitability, and floor load capacity.
Financial Institutions
Lenders use our reports to verify collateral integrity. They want to understand risk tied to aging roofs, fire protection systems, or concrete slab damage—anything that might affect loan performance or insurance coverage.
Insurance Providers
Fire, storm, and theft risks are amplified in high-volume storage spaces. Our inspections support underwriting with details on sprinkler coverage, exterior security, and roof condition.
Government & Public Agencies
Agencies using warehouses for fleet storage, supply staging, or emergency readiness must verify code compliance, energy performance, and public accessibility where required.
The Services That Deliver Confidence
We tailor each service to the unique nature of warehouse operations—high volume, high square footage, and often high stakes.
Property Condition Assessment (PCA)
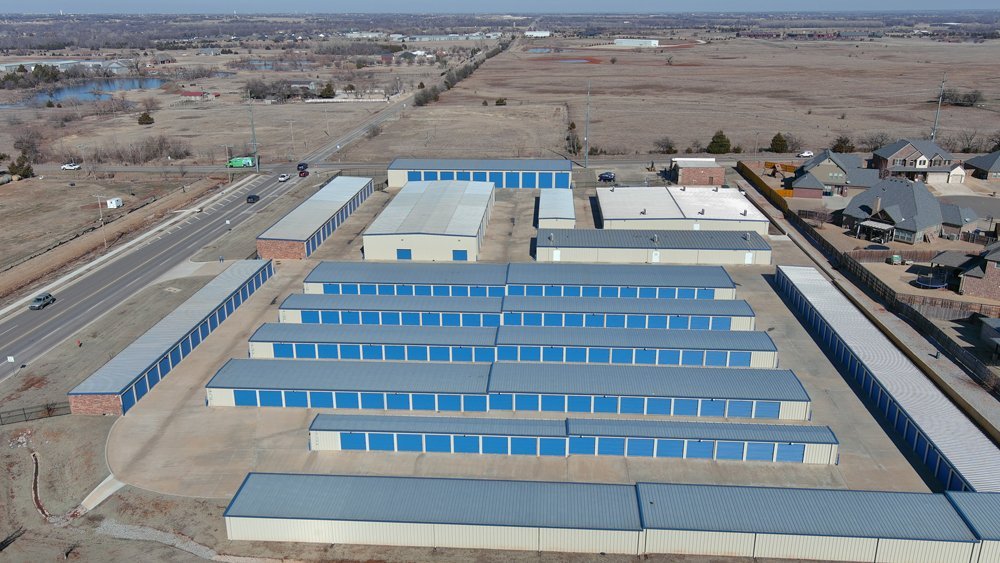
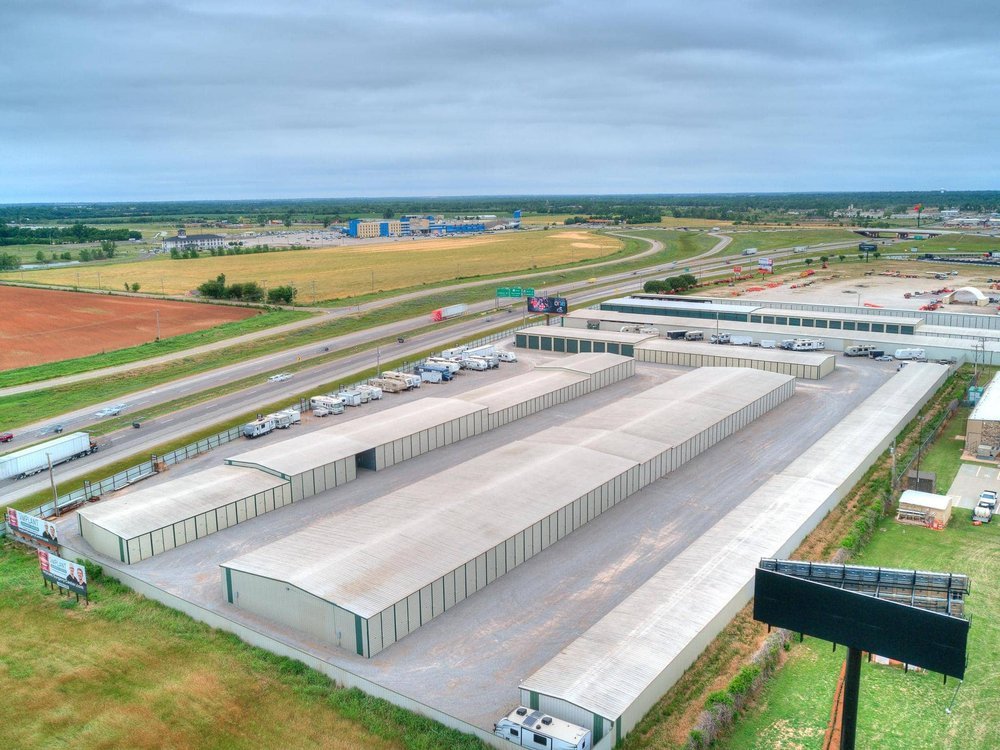
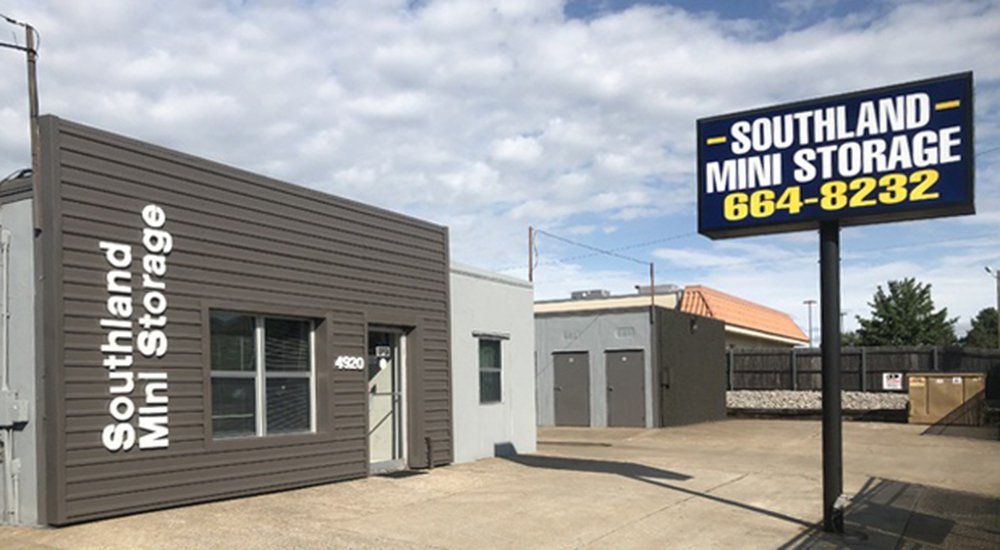
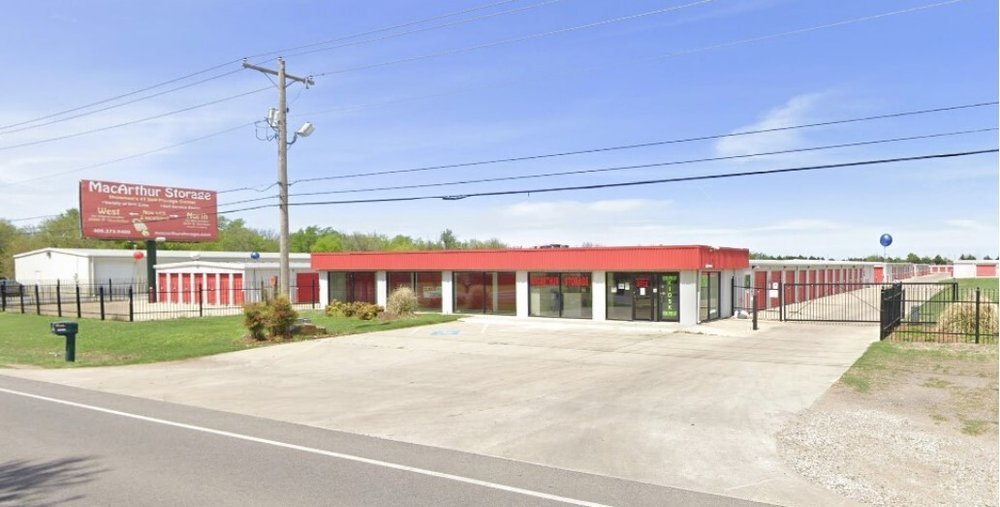
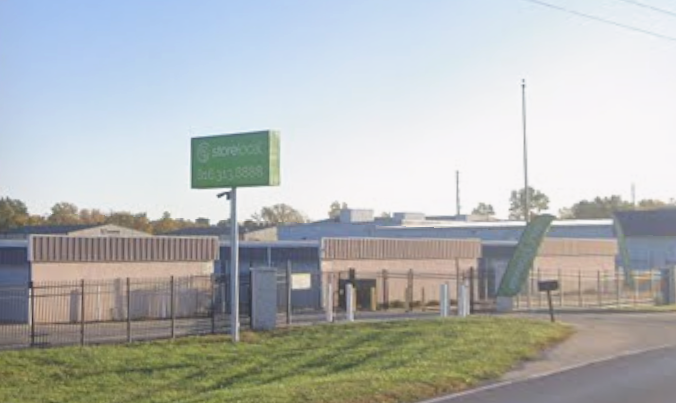
Property Condition Assessment (PCA)
For warehouses and storage facilities, our PCA includes:
Roof system integrity (membrane, metal, drainage)
HVAC and ventilation (unit heaters, warehouse fans)
Structural framing (steel frames, trusses, tilt-up concrete)
Electrical systems (lighting grids, loading dock power, panel safety)
Slab condition (cracks, control joints, forklift damage)
Fire protection (sprinklers, alarms, exit signage)
Site access (loading docks, driveways, gates, truck courts)
A Few of the Commercial Warehouses We’ve Inspected!
All findings are compiled in a detailed Property Condition Report (PCR) with annotated photos, recommendations, and life expectancy estimates.
Opinion of Cost Report
This report estimates near-term capital expenses—critical for buyers, investors, and capital planners. Typical cost projections include:
Roof membrane or coating replacement
Dock door or leveler repair
Parking lot resurfacing
Fire suppression system upgrades
HVAC or ventilation upgrades
We use local contractor estimates and RSMeans data, including a 20% pricing variance, to provide realistic budgeting ranges.
ADA Accessibility Inspection
While warehouse interiors may have minimal ADA requirements, public-facing areas like offices, restrooms, or employee breakrooms must comply. We inspect:
Parking lot and access routes
Restroom fixtures
Office entry and corridor width
Signage and handles
We follow ADA design standards and the CCPIA COMSOP to help clients limit legal risk and avoid costly post-lease retrofits.
Common Findings in Warehouse Inspections
While warehouses often appear simple, they conceal significant operational and structural concerns. Here are common findings we uncover:
Roof Drainage Failures
Flat or low-slope roofs with clogged scuppers, failing sealants, or signs of ponding that lead to water infiltration.Concrete Slab Cracking
Settlement cracks or damage from heavy forklift use, which can become safety hazards or affect storage layouts.Loading Dock Wear
Damaged bumpers, rusted doors, and misaligned levelers are common, especially in high-turnover or aging facilities.Electrical Panel Limitations
Inadequate panel capacity or outdated components that cannot meet the demands of modern warehouse automation or refrigeration systems.Insufficient Fire Protection
Sprinkler gaps in racked areas, non-functional alarms, or a lack of coverage in retrofitted mezzanine or office zones.
Some of Our Office Clients Include:
Here are a few great examples of the office buildings we’ve inspected:
Inspection Trends by Region
Each region presents its own structural and environmental challenges. Here’s what we’ve seen across the four states:
Tulsa & Oklahoma City
Aging industrial parks often show pavement failure and roof membrane wear. Drainage improvements are frequently recommended.Rogers & Fort Smith, AR
Contractor supply warehouses dominate this area. Many lack proper fire suppression or show excessive slab deterioration.Springfield & Joplin, MO
Many warehouses were converted from legacy buildings, meaning non-compliant electrical systems and uneven loading dock access.Kansas City & Wichita
Modern fulfillment centers are common but often experience premature roof wear and lack ADA-compliant office spaces.
Our inspection scope reflects these regional trends, tailoring evaluations to local needs and construction practices.
Final Thoughts: Storage That Works as Hard as You Do
Warehouses and storage buildings are meant to be durable, but durability is not immunity. A cracked slab, a leaking roof, or a failed dock can bring operations to a halt—and cut into profitability.
Our inspections give you the foresight and facts needed to avoid costly disruptions, manage risk, and invest wisely. Whether you’re purchasing, managing, or leasing, we help ensure your facility supports your business goals—not stands in the way of them.
Bibliography
Certified Commercial Property Inspectors Association. (n.d.). International standards of practice for inspecting commercial properties (COMSOP). https://ccpia.org/comsop/
International Code Council. (n.d.). International property maintenance code. ICC Digital Codes. https://codes.iccsafe.org/
National Fire Protection Association. (n.d.). NFPA codes and standards. https://www.nfpa.org/Codes-and-Standards
RSMeans. (n.d.). RSMeans building construction costs data. https://www.rsmeans.com/
U.S. Department of Justice, Civil Rights Division. (2010). 2010 ADA standards for accessible design. https://www.ada.gov/resources/2010-ada-standards/
Occupational Safety and Health Administration. (n.d.). Warehousing and storage safety. https://www.osha.gov/warehousing
Questions Answered by the Article
What’s included in a warehouse or storage facility inspection?
How does a PCA help buyers or tenants evaluate warehouse properties?
What are the most common maintenance issues found in warehouses?
How do loading dock conditions affect a building’s usability and value?
Why is an Opinion of Cost report important for warehouse owners?
What ADA features must be present in warehouse office areas?
How can an inspection reduce risk during a lease negotiation?
What safety hazards are common in aging storage facilities?
How do slab cracks and drainage issues impact operations?
What do lenders and insurers look for in warehouse inspection reports?
How do regional trends affect warehouse property condition in OK, AR, MO, and KS?
What are the fire protection requirements for large warehouse spaces?